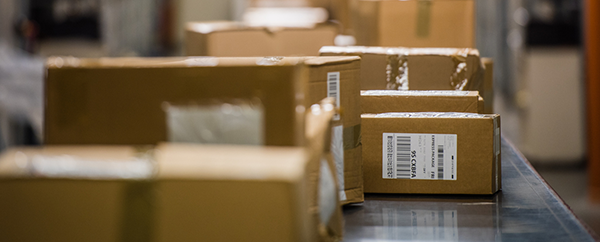
Navigating the surprising journey from drop-off to delivery
Every day, millions of packages make their way across cities, countries and even continents. From the moment you drop-off to the minute it lands on a doorstep, your package is shuffling through a labyrinth of logistics — scanned, sorted, tossed, trucked, flown, rerouted and handed off again and again. It’s a minor miracle that most make it unscathed.
But things can (and do) go wrong. Packages end up on the wrong truck. They get dropped, damaged, lost and even stolen. Understanding the journey helps you spot where things might go wrong, and how to keep your shipments safe.
Related: How to turn a shipping mishap into a customer loyalty win
What’s behind the barcode?
Tracking every move
It starts simple enough: your package is dropped off or picked up, and the carrier scans the label to enter it into the system. But this initial barcode scan is more than a receipt; it’s the package’s entry point into a sprawling logistical network.
Before reaching its destination, it’s whisked to a regional sorting center where conveyor belts, barcode scanners and robotic arms sort thousands of packages by size, weight and destination. At this stage, packages are scanned again — sometimes dozens of times — before being routed towards their next destination.
Taking the scenic route
After the initial sort, packages are loaded onto trucks, planes or even trains, depending on the distance or destination. This is the part of the journey that’s often invisible to the sender and recipient alike, but also where packages cover the most ground — likely changing hands several times.
Contrary to what you might think, your package doesn’t always take the most direct route. Carriers are constantly shifting routes to optimize efficiency, which is why two identical shipments sent on different days might end up taking completely different paths.
At any given moment, thousands of shipments are on the move — shuffling through conveyor belts, stacked on pallets or loaded into cargo holds. This leg of the journey is tightly choreographed to minimize delays, but unexpected hiccups, like weather or mechanical failures, can still throw things off track.
Reaching the finish line
As the package nears its destination, it enters the most unpredictable phase: the last mile. Here, packages move from regional hubs to local distribution centers before being loaded onto delivery trucks.
These delivery trucks pick up dozens of items bound for different addresses, zigzagging across neighborhoods to drop them off. This is where even a package that moves smoothly through the middle mile can get delayed right at the finish line.
The risk here isn’t just human error — it’s also theft, mechanical failure or routing glitches that can leave your shipment stranded.
Keeping chaos in check
Despite all the potential pitfalls that could occur between pickup and delivery, most packages make it to their destination without a problem thanks to logistics systems that are surprisingly resilient. That’s a credit to carriers investing heavily in technology to keep things moving smoothly.
Barcode scanning and tracking systems work nonstop to monitor every touchpoint, while real-time updates help catch human errors before they become problems. On top of that, warehouses are becoming smarter, integrating automation and machine learning to predict potential bottlenecks before they happen.
But it’s not a foolproof system. Even with the best technology and well-oiled systems, at every stage there’s the potential for something to go wrong.
When packages do get lost or damaged, it’s usually not due to one catastrophic failure but a series of smaller breakdowns, like a barcode that doesn’t scan correctly or a missed transfer at a hub. Plus, no amount of automation can completely eliminate the human factor: packages mishandled or mislabeled can end up nowhere near their destination.
Making smart moves
With so many moving parts, it might seem like there’s nothing a business owner can do to prevent delays or damage, but the best way to keep shipments safe is to take a proactive approach. While you can’t control every step of the journey, you can make smart decisions before your package ever leaves your hands.
Related: How to handle shipping problems like a pro
Accurate labeling is more crucial than you think. A single typo can send a package on a wild detour. Double-checking addresses, making sure barcodes are clear and confirming weight and size can all help prevent costly delays.
Packing matters just as much. Remember that using the right materials — like reinforced boxes, proper cushioning and tamper-resistant tape — can make the difference between a product arriving safely or in pieces.
And finally, there’s the reality that even the most well-packed and properly labeled shipment isn’t immune to the unpredictable. That’s where shipping insurance can add that extra layer of protection. You can’t prevent every mishap, but you can make sure that you’re not stuck covering costly replacements.
Staying one step ahead
Shipping is a modern marvel. Every package that successfully arrives on a doorstep is the result of an intricate ballet of logistics, technology and coordination. But it’s not a guarantee. Knowing how the system works — and where it can break down — helps you make informed choices that protect your business.
Related: The evolution of shipping from horseback to high-tech drone
In the end, being proactive is your best defense. From thoughtful packing and clear labeling to choosing reliable insurance, a little extra effort goes a long way. In shipping — as in business — it’s always worth being prepared.
Peace of mind starts with the right protection. Get a quote from PIP and ship with confidence!